THE VITAL IMPORTANCE OF THE OIL FILTER
THE VITAL IMPORTANCE OF THE OIL FILTER
The oil and filter must work together to protect the engine from these microscopic, abrasive metal flakes that are by-products of combustion, dirt, and dust. If you install a less effective filter, or leave a filter on too long, it can be just as bad as operating an engine with oil past its prime.
An under performing filter can negate the protection a premium oil provides, and so accelerate engine wear, affect reliability, and diminish service life. The takeaway message is that an oil’s ability to protect the moving parts in an engine from wear is only as good as the filter and its ability to remove contaminants from that oil.
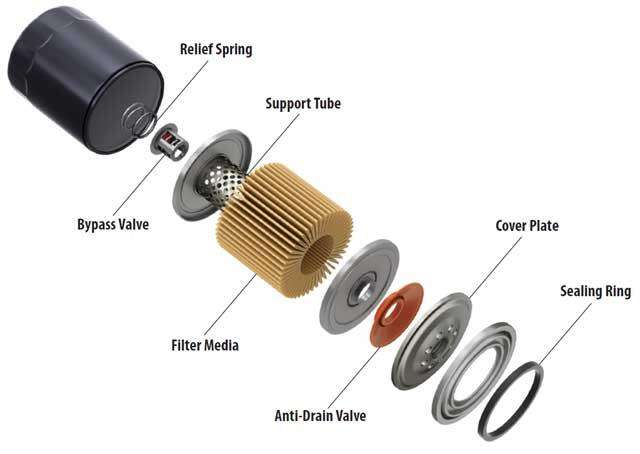
Expanded View of a Typical Oil Filter
The filter capture efficiency measures how effectively the filter removes debris from oil. A filter also has to have enough holding capacity to retain all the debris until the next oil and filter change. Vehicles that operate in dusty environments might be better off with filters that have considerably higher dirt-holding capacity or those operators might change filters more frequently.
Take care not to introduce external debris from oil fill devices. This may seem like a minor detail, but in fact, it is very important.
To better understand how a filter removes and retains particles, it’s important to understand the filter’s design and how oil moves in and out of the canister.
How Oil Flows
The filter is located between the oil pump and engine. When the engine is running, it first pulls oil from the bottom of the oil pan through a wire cloth strainer, and then pumps it to the filter. Once to the filter, the oil will pass under pressure through the smaller inlet port that forms a concentric circle around the opening at the top of the filter.
Most oil filters have an outside to inside flow. Oil starts on the outside of the pleated filter elements and flows inward to the center tube. The pleated filter medium can be made of paper, glass fibers, or a blend of both.
Inside the filter, the oil follows the path of least resistance — it first goes through the largest pores of the filter paper (media) and into the perforated center tube. Over time, as the larger pores become blocked, the oil is forced through smaller pores until all of the pores are plugged. The filtered oil will exit through the center port and on to the engine through a series of manifolds to reach different parts of the engine. Oil then flows down into the pan by gravity where it begins the journey again.
A mechanical adaptation built into engines is to reroute the oil flow when the filter gets clogged. There is a fail-safe bypass value on the engine block just in case the flow is severely reduced from a clogged filter. This allows oil to continually flow even when the filter is plugged. It’s important to remember that the oil lubricating the engine will be unfiltered when it is in this bypass mode.
Dirt-holding Capacity and Capture Efficiency
It’s true that oil moving through a filter is more or less universal, but that doesn't mean all filters are created equal when it comes to capturing and retaining debris from the oil. How efficient an oil filter is can vary sharply between manufacturers, and even between brands offered by a single company (in other words, budget-priced filters and high-performance filters). One thing is certain: Just because you see the filter described as “deluxe,” “high-performance,” “super-efficient,” or just “darn good” it doesn't mean you’re getting a premium product.
There are two criteria that influence oil filter performance and cost:
1. Dirt-holding capacity
2. Capture efficiency
Both of these properties are determined when the filter is tested using ISO 4548-12—Methods of Test for Full-flow Lubricating Oil Filters for Internal Combustion Engines. This ISO testing procedure provides important details that allow us to make side-by-side comparisons of different filters.
Dirt-Holding Capacity
A filter’s dirt-holding capacity defines how long the filter will function before it goes into bypass mode. Filters used with synthetic oils that are rated for 15,000 miles will obviously stay in use longer, so they must be able to hold more than a filter that is designed to be replaced at intervals of 3,000 or 5,000 miles. When you purchase or select a filter, one approach is to buy a filter that is rated for the miles you expect to drive between oil changes with sufficient margin for error. Don’t forget to consider dusty conditions when looking at a filter (if it will be dusty, there will be more dirt to collect).
Another approach is to find out how much debris the filter can trap. The ISO test measures the grams of debris the filter can collect before it no longer functions. You'll find large differences between filters that can capture 14 grams of dirt and those that can capture 28 grams. A filter that can hold twice the amount of debris is often more expensive.
During the ISO test, technicians progressively introduce laboratory test dust upstream of the filter. They monitor oil pressure, which will rise slightly as the filter loads with dirt. Once it reaches the terminal pressure drop (determined by the filter maker), they terminate the test. They calculate the total amount of dirt removed by the filter from the total amount that they introduced.
Capture Efficiency
Another important measure of oil filter quality is known as the beta ratio. This measure describes the filter’s particle capture efficiency at different sizes. Manufacturers use different average pore sizes for the filter’s media. The media require finer pore sizes to remove the smaller, micron-sized particles. Those finer pores can be more expensive than coarser media that have larger pores.
The test conditions for determining the beta ratio are the same as the conditions for the capture efficiency. The two tests occur at the same time. During the test (done on a laboratory test stand), oil flows from the test reservoir though the filter and back to the same reservoir.
While technicians add the controlled stream of laboratory test dust, a pair of special sensors (called particle counters) are positioned upstream and downstream of the filter. Because the filter removes particles of various sizes, the concentration of particles that are upstream of the filter will always be higher than the concentration downstream.
The beta ratio is the ratio of these two concentrations:
For any given particle size (such as 10 micrometers) the higher the beta ratio, the better the filter’s capture efficiency. For instance, if ten particles greater than 10 microns (micrometers) are counted upstream of the filter and only one of these particles is counted downstream, then the beta ratio is 10 (10/1).
You can convert the Beta Ratio to efficiency as:
The beta ratio and the capture efficiency have no value unless we know precisely the size of the microns being evaluated in the test (10 microns for instance). Working film clearance between the piston ring and cylinder wall in engines is extremely small — maybe as little as 10 microns. Debris in the 10-micron range can cut or scratch metal as the particles roll between opposing surfaces. Particles larger than 10 microns will not fit into the smaller gaps and will be swept aside. Smaller particles will generally flow through the gap with the oil.
Consider that a standard oil filter removes particles that are larger than 40 microns. It’s been demonstrated that particles that average 10 microns can produce four times more wear on rods, rings, and bearings than particles larger than 20 microns.
Can you see the problem?
General Motors reported that a filter that captures 30-micron particles or larger reduced engine wear by 50 percent over a 40-micron filter. A 15-micron filter reduces engine wear by 70 percent over a 40-micron filter.
This is why experts often measure and report capture efficiency based on how well the filter removes 10-micron particles or larger. It is worth noting that this performance property is a large component of the premium price you’re paying for high-end filtration.
Back to the capture efficiency. A filter that has a 95 percent capture efficiency of particles larger than 20 microns means it will remove 95 percent of particles that are equal to or larger than 20 microns on a single pass.
Table 1. Beta Ratio and Efficiency
Experts generally agree that an oil filter should have a beta ratio of 100, which is a 99 percent capture efficiency for 10-micron or larger particles (100-1/100 = .99 x 100 = 99%; see Table 1).
Unlike the markings on an oil container, finding information about a filter’s beta ratio and capture efficiency is often difficult to locate on the filter’s package or manufacturer’s website. Most likely, you will have to ask the supplier for the capture efficiency and beta ratio of the filters you purchase. But the answer to this single question could greatly prolong the life of your equipment.
Properly Dispose of All Products
It goes without saying that we all need to dispose of used oil and oil filters so that we do not contaminate land or water. One quart of oil has the potential to contaminate up to 250,000 gallons of drinking water or produce an oil film over a 2-acre pond. With the high risk for affecting water, mismanaging used oil drained from an engine or oil remaining in a filter or jug is not an option.
Always completely drain oil containers and filters before dispensing of them in in the trash.
Everyone should store used oil for proper disposal.
The key to properly managing oil filters is to completely drain them before disposal.
Even small actions (such as making sure that you completely drain devices or funnels) will help keep the environment cleaner.
Conclusion
The oil and filters you choose greatly affect your equipment’s reliability and life expectancy.
If you intend to run equipment to the end of its useful life or extend its normal service life, then you really need to educate yourself about the oils and filters you use in that equipment. Consider the money you have invested in purchasing trucks, sprayers, mowers, planters, combines, and other equipment. That investment should convince you that knowing more about the oils and filters you use to protect that equipment is a high priority.
You can go cheap and save money now. But in the long run, it may cost more when your equipment breaks down and is prematurely damaged due to the wrong oil or and under performing filter.
You can just as easily overspend on exotic oils and fancy oil filters that deliver little return on investment — or the benefit will only be gained by the next owner of the equipment after you sell it.
This is why it is important to remember: Select lubricants more on what the lubricant is designed to do rather than its cost.
Think performance first, price second. By making better selections, you should expect increased fuel economy, lessened emissions, and extended life expectancy of equipment.
Oils have come a long way since the 1960s. They last longer and maintain their viscosity better under strenuous conditions. But choosing the wrong oil for the wrong application can be costly. Read the owner’s manual for your vehicle to be sure you purchase oil, and realize what all the numbers on the jug of oil mean before you dump just any old oil into your equipment.
Going cheap and saving money in the short run may cost you big in the long run